Automated workflow solutions
Maintain overview – increase performance – reduce costs
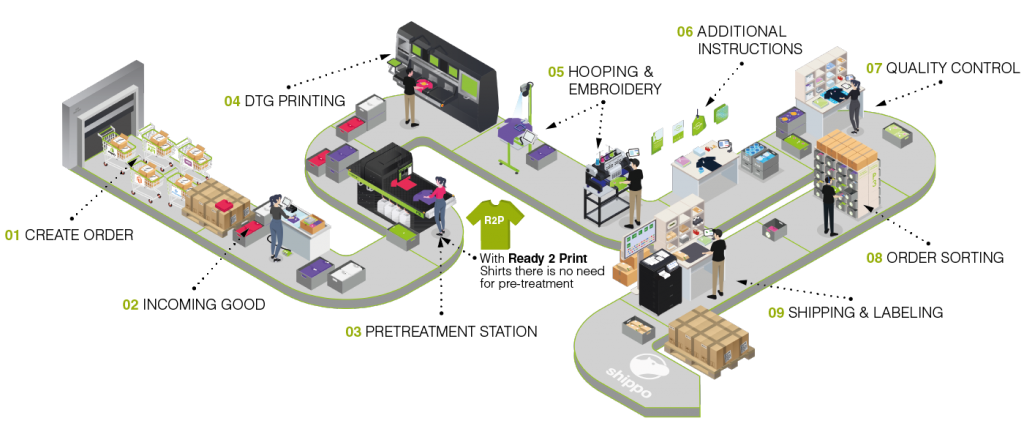
Higher production efficiency through automation
Our DTG machines make the integration into popular e-commerce providers like Shopify™, Shopware™ along with social media marketplaces like Instagram™, Facebook™ easier than ever before. They make the shop floor processes and production process efficient and fast. Implementing a barcode system which will eliminate errors and keeps the data locally for increased security is an additional advantage. Our systems will scale with the business and production and production development of our customers.
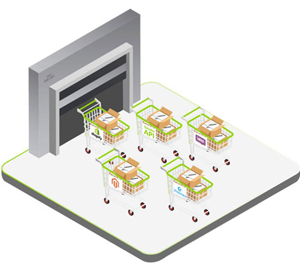
01 – Orders are received
Orders can reach you in different ways – be it from customer service, via API interface or various existing customer stores. The orders are generated digitally, where all order-related information is contained. Confusion of the production files is thus impossible.
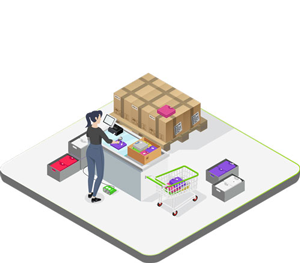
02 – Goods receipt
The terminal at the goods receipt ensures that the right goods are kept ready for the orders. At this station the textiles also receive their QR code with all information about the order.
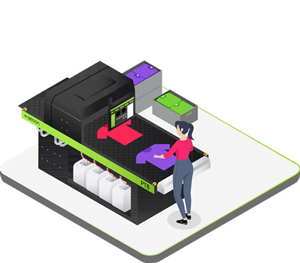
03 – Pretreatment
Which textile side must be pre-treated at which point and how large will? The Pretreatment Terminal provides this and other information fully automatically.
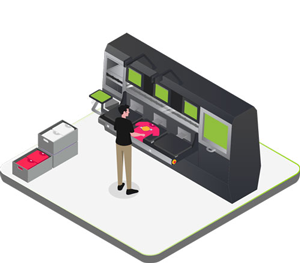
04 – Digital textile printing
Automatic loading of print files of jobs, control of positioning via EPS and saving of machine profiles per item and even per color. Maximum error reduction – no more wrong motif on the textile!
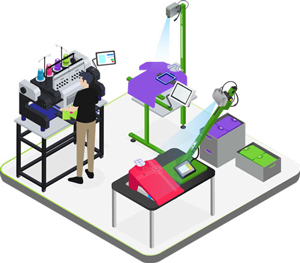
05 – Finishing techniques
Do you offer your customers additional finishing techniques such as embroidery, appliqués, laser engraving, rhinestones or rivets? No problem, these machines can also be easily integrated into the automated production process.
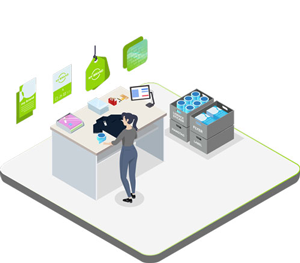
06 – Additional order instructions
At this station, additional instructions such as adding flyers, attaching additional stickers, pressing on transfers or other instructions during production can be controlled automatically.
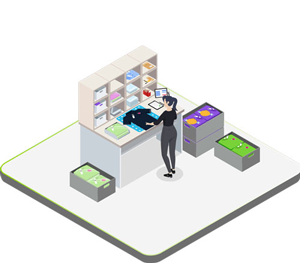
07 – Quality control
The system helps you to avoid production errors in time and transparently stores all activities of your production. If not all refinements are completed, further processing is blocked. This applies to all stations and can also be viewed by your account manager. Errors become transparent. Using RFID, even the history of textiles could be traced for a lifetime. The digital signature dramatically improves quality compared to conventional production.
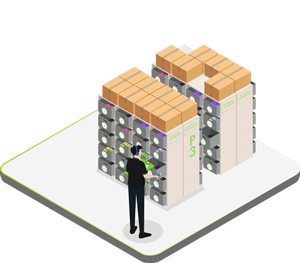
08 – Automatic sorting by QR code
No matter whether you produce in a structured, orderly or chaotic way. The system helps you to sort your orders. Simply scan the ID tag and use the intuitive “Sort by voice” function – the system will automatically guide you to the correct order field. Only after the last part has been scanned, the order is released.
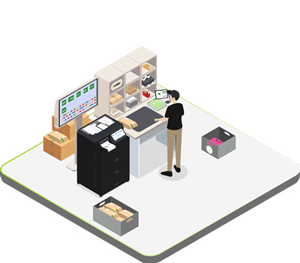
09 – Preparing the goods for shipment
Regardless of whether DHL, UPS or any other shipping service provider, the system does the work and automatically prints the package contents and shipping label including all necessary customs documents. If an article is incorrectly sorted, the system will block it. Only after the last part has been scanned, the operator can send.
Connect front-end and back-end processes
Individuality and flexibility are the demands made on todays textile printer. This requires the conversion of the entire production workflow. It is important that each station from online ordering to production and shipping can be assigned correctly and that communication runs smoothly. By cooperating with Smake® or Kothari® aeoon can offer a complete software solution that connects the entire workflow.
The front-end processes of an e-commerce platform can be linked to the clients production fleet and production workflow. Every step from the customers print order to the delivery of the product can be seamlessly automated at Industry 4.0 standard within a few minutes. aeoon clients can create their own e-Shop according to their specific target group, thanks to the integrated software in the printers.
Optimization
The production process can be easily controlled and monitored by statistics received from the printer. Hence it is possible to analyse the performance, reduce errors and production stops. All aeoon DTG printers can be integrated into an automated production workflow.
Information graphic of the automated production workflow
Color IOS – Color ink optimization system
Reduce your white ink usage and the print costs by about 30% with our advanced RIP offering. This add-on considers the background color of the textile even more, by using it as an ink and adapts the amount of white ink needed for the underbase to print the motif. Depending on the design, the savings can be of up to 30% ink saving, making this software a must have for the DTG industry and a great add on.
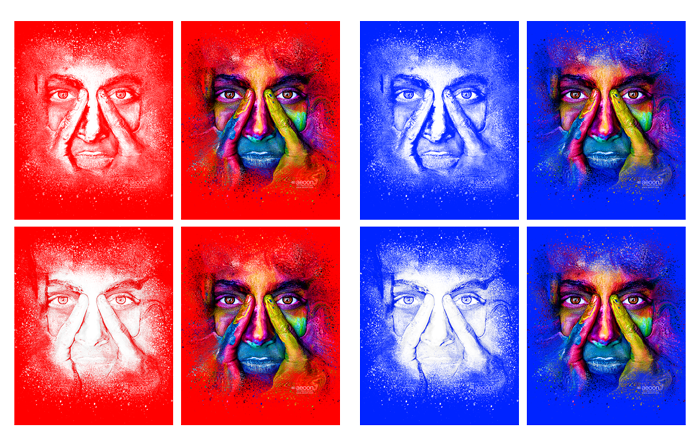